Seu programa de manutenção precisa de… bem, manutenção?
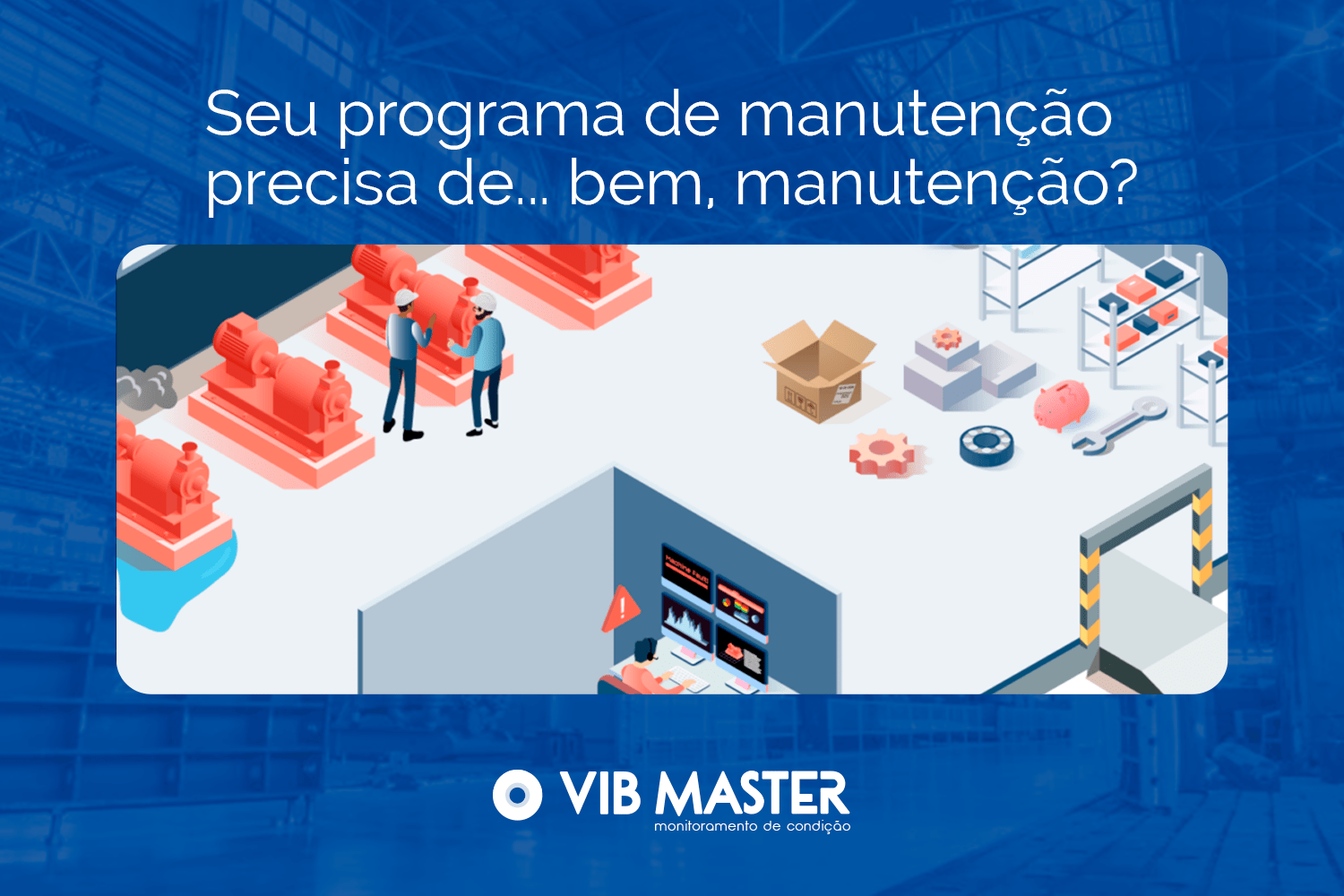
Um “bom” programa de manutenção envolve manter o equipamento em condições de pico e mitigar falhas. Chegar a esse resultado requer o equilíbrio adequado de estratégias, pessoas e recursos. Entre mudanças na administração, a porta giratória de funcionários e contratados não confiáveis, pode ser relativamente fácil para o programa de uma organização passar de “bom” para um ciclo reativo de destruição.
O objetivo desta postagem no blog não é fazer você se sentir mal com sua situação atual de manutenção – é uma intervenção para os indivíduos ou organizações que podem se sentir empacados. Muito parecido com um programa de 12 passos, o primeiro passo é admitir que você pode ter um problema. O objetivo aqui é ajudar a reconhecer os sinais do que torna seu programa ineficaz para que você possa ser proativo.
Sinal 1: Falha da máquina sem aviso
Um dos indicadores mais evidentes de um programa de manutenção ineficaz é aquele que possui uma estratégia geral de manutenção reativa em que as máquinas falham sem aviso prévio (também conhecido como “Manutenção de quebra”). A mentalidade desse tipo de estratégia é deixar as máquinas falharem e reagir aos problemas quando eles ocorrerem.
O que há de errado com isso? Para começar, isso pode levar a custos de manutenção muito altos de várias formas – falhas de máquina negligenciadas podem causar danos secundários, tempo de inatividade da produção, horas extras para funcionários/contratados e aumentar o custo de manter as peças sobressalentes disponíveis. Uma abordagem reativa é uma entrega de controle para sua organização, ativos e normalmente se presta a uma cultura de manutenção ruim.
A resposta para esse problema é detectar problemas críticos de ativos antes que eles ocorram (“Manutenção Preditiva” ou “PdM”). Mudar para esse tipo de estratégia permitirá a você a liberdade de agendar sua manutenção, solicitar suas peças de reposição com antecedência e agir antes que os problemas se transformem em algo mais.
Sinal 2: Dados de vibração, mas sem análise
As equipes de manutenção e confiabilidade precisam de profissionais com experiência necessária para interpretar dados de vibração. Você pode coletar dados em suas máquinas o dia todo, mas os dados não servirão se você não souber o que fazer com eles. Sem mencionar que as equipes geralmente são pressionadas a gastar menos tempo analisando dados e apenas obter respostas sobre o que precisa ser feito e como fazê-lo o mais rápido possível.
Além disso, os dados da máquina precisam ser armazenados em um local centralizado. Isso mantém todas as partes interessadas internas alinhadas, evita a execução de manutenção desnecessária e garante que sua equipe fique por dentro da manutenção necessária. A coleta e o rastreamento de dados acionáveis são bastante desafiadores sem experiência, ferramentas e tempo.
A aceitação que você recebe da alta administração permitirá que você invista em equipamentos de monitoramento de sensores e CMMS (software de gerenciamento de manutenção computadorizada). O CMMS ou outro software especializado irá ajudá-lo a criar modelos preditivos e informar as decisões, ações ou inações a serem tomadas durante a manutenção do maquinário. No entanto, esses investimentos às vezes podem representar um obstáculo em seu orçamento. É fundamental entender que se você investir em PdM, seus técnicos receberão treinamento. Sem o conhecimento adequado no chão de fábrica, você estará jogando dinheiro pela janela.
Sinal 3: Não ter as peças certas a tempo
Conforme abordamos anteriormente no post – não ter as peças sobressalentes adequadas quando ocorre uma falha na máquina pode aumentar a duração do tempo de inatividade. A resposta para este problema não é apenas encomendar um monte de peças sobressalentes e tê-las à mão (geralmente é isso que os programas de Manutenção Preventiva fazem).
Por que? Porque o custo de pedir peças sobressalentes regularmente pode aumentar rapidamente e deixar sua organização com prateleiras cheias de coisas que não são necessárias. Além disso, os programas de manutenção com uma estratégia preventiva geral tendem a substituir os componentes da máquina que não precisam ser substituídos.
O curso de ação apropriado com peças de reposição é encontrar um equilíbrio com o reabastecimento de seu estoque. Assim que você detectar falhas na máquina, programe quando os reparos ocorrerão e solicite as peças de reposição de acordo. Tê-los antes do previsto irá prepará-lo para o sucesso.
Sinal 4: Sensores e ferramentas abandonados
Nos últimos anos, os sensores de vibração sem fio tornaram-se comuns em muitas instalações. Aqui na VIBMASTER, nós amamos sensores sem fio tanto quanto qualquer um, porém, eles só agregam valor se os dados de vibração que eles estão registrando estiverem sendo utilizados. Se você tiver esses tipos de sensores em seus ativos, certifique-se de que a empresa de serviços com a qual você fez parceria está analisando os dados coletados e se comunicando com sua equipe para tomar medidas de manutenção corretiva.
Da mesma forma, outro problema que às vezes encontramos na indústria é o fenômeno das ferramentas abandonadas. Um exemplo é quando uma organização investe em equipamentos de monitoramento de condições que pretende usar internamente, mas acaba sendo negligenciado. Isso pode ocorrer por vários motivos:
- Ninguém sabe usar o equipamento por falta de treinamento, conhecimento ou experiência.
- O funcionário ou contratado que sabia como usar o equipamento deixou a organização – talvez tenha se aposentado ou mudado de emprego.
- Uma mudança de mãos na liderança e/ou tomadores de decisão – a decisão infeliz pode ter sido tomada em algum momento para se afastar do monitoramento de condições.
A solução para esses problemas é garantir que o equipamento preditivo da sua organização esteja operacional, em uso e forneça à sua equipe os insights acionáveis necessários para que ela seja produtiva.
Sinal 5: Escassez de Habilidades, Mudanças de Pessoal e Contratantes Ruins
Encontrar profissionais de manutenção e confiabilidade altamente qualificados pode ser bastante desafiador. A falta de especialização é um problema ainda causado por empresas que não investem em treinamento para os funcionários que possuem. É aqui que a falta de experiência pode se confundir com a falta geral de dinheiro. Sempre que falta financiamento para ferramentas e pessoal, não é incomum que não haja financiamento para o treinamento necessário para desenvolver as habilidades dos funcionários.
Quando uma instalação contrata um empreiteiro para gerenciar seu programa de manutenção, normalmente o fornecedor mais barato vence a licitação. No entanto, a contratação de empreiteiros baratos geralmente tem um custo. Custos mais baixos podem ser uma indicação de que o empreiteiro não é tão qualificado quanto seus concorrentes. Quando o empreiteiro carece de habilidades, sua instalação experimentará os pontos problemáticos associados à falta de experiência, conforme descrito acima.
Qual é a solução? Procure o empreiteiro certo, defina expectativas claras com antecedência e certifique-se de que ele está fornecendo o que foi acordado contratualmente. Mesmo que seu orçamento seja apertado, sempre encontre espaço para investir em seus funcionários por meio de treinamento. Seu crescimento abrirá novas oportunidades para sua equipe e organização crescerem também.
Como ser mais eficaz
Se você está lutando com um ou mais dos problemas que abordamos nesta postagem do blog, você não está sozinho. Algumas soluções importantes para todos esses problemas estão nos marcadores abaixo:
- Implemente estratégias de manutenção preditiva (PdM) para ativos em suas instalações para detectar problemas e corrigi-los antes que ocorram problemas adicionais.
- Certifique-se de que seus dados de vibração estão sendo analisados e forneça à sua equipe de manutenção as informações para tomar ações corretivas.
- Não espere até que ocorra um problema para solicitar peças sobressalentes. Além disso, não peça peças de que não precisa. Em vez disso, encomende o que for necessário e agende sua manutenção conforme as falhas da máquina forem detectadas.
- Certifique-se de que os sensores de suas máquinas estão fornecendo dados e certifique-se de que seus funcionários saibam como usar as ferramentas nas quais sua empresa investiu.
- Não deixe que empreiteiros ruins sobrecarreguem você ou sua equipe – certifique-se de comprar antecipadamente e fazer parceria com os empreiteiros apropriados.
- Invista nas pessoas que trabalham para você treinando-as e construa uma cultura de crescimento!
A solução mais importante para todos os problemas que abordamos neste post é a mentalidade. Uma equipe de manutenção não existe apenas para corrigir problemas. Se essa mentalidade for adotada, isso servirá como um convite para uma equipe ficar presa em um ciclo reativo de destruição.
Nós não podemos APENAS CORRIGIR. A manutenção eficaz e confiável é muito mais – detecta problemas, corrige-os e verifica as correções. Envolve a conclusão de tarefas com precisão e atenção aos detalhes. Envolve boa organização, programação e uma devoção para melhorar.
Quer saber mais sobre Boas Práticas de Manutenção Preditiva? Não deixe de acompanhar o nosso blog e nossas mídias sociais. Além disso, confira nosso Programa de Transferencia de Tecnologia se estiver procurando resolver alguns dos problemas que abordamos neste post. Estamos aqui para ajudar, no que pudermos.