Aprenda como acabar com as paradas de máquina inesperadas na sua empresa
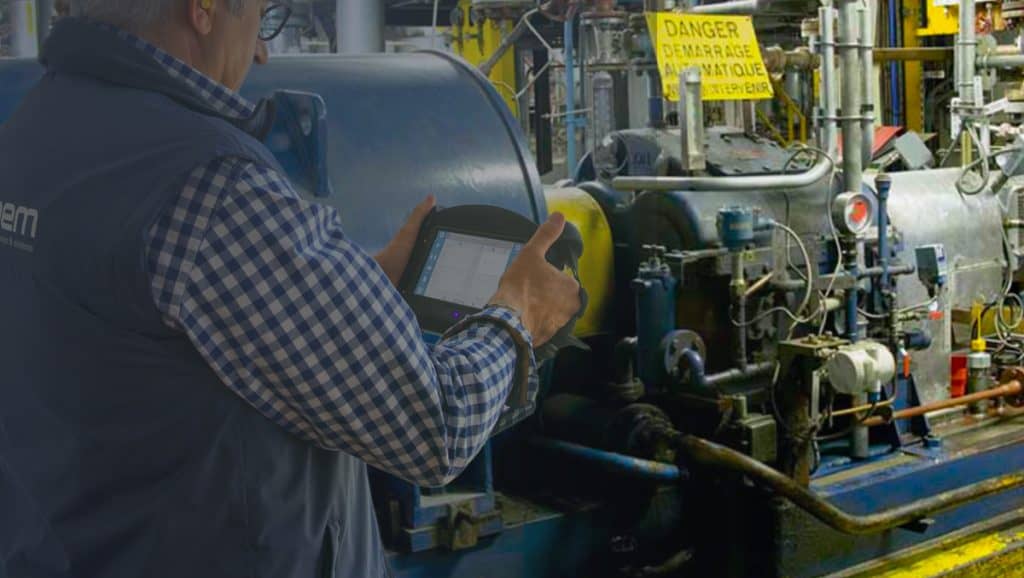
Otimização da eficiência de um programa de monitoramento de condições, graças a um sistema especialista com indicação do nível de confiança.
ANÁLISE DE VIBRAÇÃO: uma tarefa que demanda grande empenho
Todo programa de monitoramento de condições começa por uma classificação das máquinas, de forma a determinar a qual das máquinas da fábrica o programa é aplicável, e como elas serão monitoradas. Esta classificação depende de vários critérios, tais como:
- Quão crítica é a máquina para o processo (a que ponto o processo é dependente desta máquina)
- Que falhas estamos tentando prevenir, qual é a possibilidade de detecção, como podem ser detectadas e com que antecedência podem ser detectadas
- Quanto tempo será necessário para reparar a máquina
- Desafios da manutenção, associados ao reparo (gerenciamento de peças sobressalentes, operações da manutenção que necessitam de recursos específicos, tais como gruas…)
Uma vez incluída a máquina no programa, será necessário monitora-la para prevenir falhas inesperadas. Isto implica que mesmo uma máquina em bom estado será vigiada de perto.
Entre as várias técnicas de monitoramento de condições atualmente disponíveis, a análise da vibração é sem dúvida a mais usualmente utilizada. A análise da vibração compreende várias etapas, incluindo as próprias medições e sua efetiva análise. Uma abordagem padrão dos dados de vibração inclui a revisão sistemática de cada máquina que faz parte do programa. Além do tempo exigido, na maioria das vezes isto resulta numa análise que não era prioritária. Na maioria dos casos, cerca de 70 a 80% das máquinas em um programa, estão em bom estado, seja em qual for o momento.
E se existisse, uma melhor maneira, que permitisse ao programa de monitoramento de condições se concentrar somente nos casos críticos?
Passo-a-passo de implantação para Engenheiros e Supervisores de Manutenção
A – Um objetivo comum: Aumentar a confiabilidade com recursos limitados
Uma vez estabelecido o programa, a oportunidade de melhoramento reside principalmente na mudança da estratégia de medição. Isto pode ser obtido investindo em mais sistemas (por ex. adicionando o monitoramento Online), e/ou adicionando mais pessoas à equipe para obter uma maior vigilância das diferentes máquinas (por ex. aumentando a frequência das medições e análises).
Todos os programas de monitoramento de condições são limitados pela capacidade de expansão dos recursos de instrumentos e seres humanos. Este documento apresentará soluções que permitem melhorar a eficácia do programa de monitoramento de condições sem exigir recursos adicionais.
B – O que diz a norma ISO10816?
No mundo da análise da vibração, a norma ISO10816 de “Avaliação da vibração da máquina por medição em partes não-rotativas” é dificilmente questionável. Fornece instruções claras para as medições de vibração a serem realizadas e os limites a aplicar, segundo a classe da máquina (potência, velocidade, tipo de montagem…). Vários fabricantes de máquinas industriais (OEM) utilizam a norma ISO10816 em seus procedimentos de manutenção e em suas recomendações.
A norma ISO10816 não fornece nenhuma ajuda na definição dos diagnósticos e das falhas presentes na máquina, mas oferece recomendações gerais quanto ao estado global da máquina: Baseando-se no valor da medida da velocidade da vibração, é possível avaliar o risco de falha segundo a classe da máquina.
C – O que diz o analista de vibração?
O analista de vibração deverá se apoiar sobre a identificação das falhas para fornecer recomendações de manutenção e planificar e orientar da melhor maneira as ações de reparo. Todos os analistas de vibração estarão de acordo com a seguinte declaração: Se o nível de vibração for conforme à norma ISO10816 e se não houver choques na máquina, esta máquina está em boas condições.
Se esta condição não se verificar, ele irá então efetuar uma análise mais aprofundada dos dados de vibração, à procura de sintomas para tentar identificar falhas na máquina e fornecer recomendações de manutenção baseadas na sua avaliação do risco, como agiria um médico em relação a um paciente para diagnosticar sua doença e dar as melhores recomendações para o curar.
Diagnóstico Automático através da Inteligencia Artificial
“Em inteligência artificial (IA), um sistema especialista é um sistema de computador que emula a capacidade de tomar decisões de um especialista humano. Os sistemas especialistas são concebidos para resolver problemas complexos raciocinando sobre conhecimento, representado em primeiro lugar por regras if-then (se – então) em vez de utilizar um código procedural convencional” (fonte Wikipedia)
Aplicado a nosso campo, um sistema especialista utilizaria a IA (para estabelecer um diagnóstico automático das máquinas rotativas. O sistema especialista terá que revisar automaticamente cada espectro e forma de onda do tempo, bruto (estado natural, não processado) para identificar e avaliar a severidade de cada falha. Ele as apresentará de modo priorizado, segundo o nível de confiança atribuído a cada falha detectada, o que também permitirá priorizar as ações de manutenção a realizar. Além disso, como um especialista humano, ele será capaz de não somente indicar as falhas detectadas, mas também de fornecer uma avaliação global dos riscos e indicar ao usuário (operação) se uma ação imediata precisa ser executada.
E – Soluções para melhorar a eficiência de um programa de monitoramento de condições com os recursos existentes
É possível hoje ajudar os usuários especialistas a se concentrar sobre as máquinas críticas, graças à utilização de um sistema especialista adequado. Para alcançar este objetivo, este sistema deverá fornecer as seguintes informações:
Nível de criticidade (sinalizadores), VERDE – AMARELO – VERMELHO: foco nas máquinas críticas
Avaliando o estado global da máquina e apresentando os resultados de uma forma simples, como bandeiras (sinalização) VERDE, AMARELA ou VERMELHA, o sistema especialista pode ajudar o especialista humano a priorizar sua análise:
- Não é necessário verificar as máquinas em VERDE
- Começar pelas máquinas em VERMELHO
- Revisar as máquinas marcadas em AMARELO em uma segunda etapa.
A melhor solução reside em sistemas que podem levar em conta:
- A norma ISO10816.
- A presença de choques
- E como um especialista, avaliar os riscos baseando-se nas falhas e nos sintomas detectados
Por exemplo:
- Um defeito de desbalanceamento pode ser diagnosticado com um alto nível de vibração em uma máquina, mas dependendo do equipamento, pode não exigir necessariamente uma ação imediata.
- Por outro lado, a acumulação de múltiplas falhas em uma dada máquina, mesmo que cada falha isolada não apresente o mais alto nível de severidade, pode representar um risco importante para essa máquina, e exigir uma atenção imediata.
Indicador do nível de confiança: exige uma ação, ou simplesmente uma orientação para diagnósticos?
Fornecendo um resultado de diagnóstico automático é uma coisa boa, mas se um defeito detectado com um alto nível de confiabilidade for representado exatamente do mesmo modo que um defeito detectado com um baixo nível de confiabilidade, isto pode fazer o usuário perder a confiança e ser forçado a verificar cada resultado fornecido pelo sistema automático. Isto não ajudaria de maneira alguma a melhorar a eficiência do programa.
A melhor solução é utilizar um sistema com uma abordagem baseada nos sintomas (como faria um especialista) e que seja capaz de caracterizar a probabilidade de presença de falhas baseada nos sintomas detectados. A melhor solução de IA identificada atualmente é a rede Bayesiana, que considera integralmente um processo de ponderação e utiliza melhor a experiência adquirida num dado campo de aplicação.
“Bayesiano” tal como definido no dicionário Merriam-webster: “sendo, referindo-se a, ou envolvendo métodos estatísticos que atribuem probabilidades ou distribuições a eventos (como chover amanhã) ou parâmetros (como uma média da população) baseados em experiência ou nas melhores suposições antes da experimentação e coleta de dados e que aplica o teorema de Bayes para revisar as probabilidades e distribuições após a obtenção de dados experimentais”
Cada falha pode ser caracterizada por sintomas. Exemplos de sintomas podem ser:
- Um valor de vibração em velocidade global considerado elevado
- A presença de choques
- A temperatura do mancal considerada elevada
- A evolução da falha, comparada à medição anterior, considerada elevada
Exatamente como um analista da vibração, e sistema especialista irá procurar estes sintomas, e computar a probabilidade da presença de um defeito, com base na probabilidade de cada um dos sintomas de fazer prever o defeito.
O exemplo abaixo ilustra um defeito de desbalanceamento. O desbalanceamento é indicado por diversos sintomas que podem ser encontrados nos dados de vibração, alguns sendo mais importantes que outros. A direção de medição, na qual os sintomas foram encontrados, também pode ter um impacto sobre a probabilidade de presença do defeito.
Além disso, a probabilidade de presença de cada sintoma simples pode ser calculada através de um algoritmo que ponderará o resultado, como na sigmoide (formato Sigma, S) abaixo apresentada.
Quando um valor de um indicador X < “S1” é projetado através da sigmoide, a probabilidade do sintoma resultante (valor entre 0 e 1) estará abaixo de 0.60. Por outro lado, um valor de X > S2 projetado na sigmoide permanecerá próximo de 0.90. Esta abordagem evita as limitações básicas de uma simples ultrapassagem de limiar. Em outros termos, 1.01 é realmente um valor perigoso para um dado indicador, quando 0.99 está OK?
Com tal abordagem, o nível de confiança associado a cada falha pode ser apresentado com grande precisão O utilizador pode então determinar muito facilmente se o resultado automático deve levar a uma ação imediata, ou se deve apenas ser tomado como uma ajuda para identificar o melhor diagnóstico;
Fornecer ao pessoal de manutenção resultados automáticos e instantâneos
Uma outra forma de aumentar a eficiência de um programa de monitoramento das condições consiste na solução seguinte. Com um sistema especialista fácil de utilizar, apto a fornecer resultados instantâneos diante da máquina.
- Pode-se ganhar tempo, já que os resultados podem ser interativos, o que evita deslocamentos múltiplos e procedimentos burocráticos para empreender ações. Por exemplo, se for detectado um problema de rolamento ou de lubrificação, a recomendação automática pode ser: “lubrifique primeiro a máquina, se seu desempenho não mudar, planifique a substituição dos rolamentos”
- Outros controles (medições) podem ser realizados por outra equipe de manutenção, não necessariamente pertencente ao departamento de manutenção e confiabilidade. Se uma máquina apresentar um comportamento suspeito (ruído, temperatura), é fácil verificar a máquina e chamar o especialista apropriado
- Controles adicionais (medições) podem ser realizados por outra equipe de manutenção nas máquinas que não fazem parte do programa: Com um resultado automático de alto nível de confiabilidade, o pessoal estará capacitado a tomar uma decisão sem a ajuda do especialista, que poderá então se focalizar unicamente sobre as máquinas que fazem parte do programa de monitoramento das condições.
Configuração fácil e confiável do sistema
Finalmente, mas não menos importante, um pré-requisito para que tal solução seja realmente útil reside em sua facilidade de configuração. Numerosos sistemas especialistas falharam, no passado, não devido a sua precisão, mas devido a sua complexidade de configuração. O que adiantaria ter um sistema dito especialista, se somente um especialista do próprio sistema especialista for capaz de o configurar corretamente, e o ajustar, segundo o tipo de máquina?
O sistema especialista deve ser capaz de determinar ele mesmo quais são as medidas a obter segundo o tipo de máquinas (tipo de componentes, velocidade, potência, tipo de montagem, etc.) de maneira a fornecer sempre os resultados automáticos mais precisos e isto, em um prazo de poucos minutos. Você não terá que perder mais tempo do que isso se seu pessoal de manutenção estiver capacitado a realizar facilmente o controle do estado dos equipamentos suspeitos, mesmo que estes não façam parte do programa de monitoramento das condições.
F – Resumo
Sistemas especialistas que fornecem diagnósticos automáticos de máquinas rotativas são uma solução simples e eficaz para melhorar a eficiência de um programa de monitoramento das condições, sem recursos adicionais. Os requisitos do sistema para oferecer tal desempenho são:
- Fornecer um meio simples e confiável de configurar o sistema especialista, que possa ser executado em poucos minutos por um pessoal de qualquer nível de conhecimento ou especialização.
- Oferecer um primeiro nível de avaliação dos riscos, para que o especialista possa priorizar suas análises e se focalizar sobre as máquinas críticas.
- Fornecer um nível de confiabilidade associado à detecção da falha, para que esta possa se converter imediatamente em ação, ou ser utilizada como uma orientação para a análise posterior.
- Oferecer resultados instantâneos para que uma ação direta, possa ser empreendida sem a ajuda de um especialista, nas máquinas que fazem parte de um programa de monitoramento das condições.
- Assegurar resultados instantâneos permitindo que outras equipes de manutenção possam facilmente efetuar controles (medições), de maneira autônoma, em máquinas que não fazem parte do programa de monitoramento das condições.
Com o aperfeiçoamento da eficiência de seu programa de monitoramento das condições, um tempo de produção adicional pode set obtido e os custos de manutenção e confiabilidade serão continuamente otimizados.
Sobre os autores
Brian SHANOVICH
Brian tem estado envolvido com tecnologias de confiabilidade há mais de 25 anos. Como Gerente de Produtos da VibrAlign e anteriormente como gerente de vendas, Brian viaja o país para educar sobre o valor do alinhamento de precisão. Brian está agora a cargo da linha OneProd de soluções inteligentes de monitoramento das condições para o mercado norte-americano, promovendo ativamente o FALCON, EAGLE e MVX.
Patrick LABEYRIE
Patrick é o diretor da marca ONEPROD de soluções de monitoramento de condições da ACOEM. Chefe do departamento de produtos e serviços desde 2012, ele começou sua carreira 30 anos atrás como engenheiro de vibração na área da atenuação acústica de máquinas rotativas para submarinos. Dedicou então seu trabalho ao diagnóstico e monitoramento de máquinas rotativas numa ampla gama de indústrias, durante a evolução da empresa ACOEM. Em 2007, foi reconhecido como perito pela indústria nuclear francesa com o grupo AREVA, em Mecânica e mecânica dos fluidos, Dinâmica, por ex.: vibrações, ruídos, sísmicos, impacto, Fábrica/Equipamento – Sistema de Controle e Gerenciamento, Sistemas de Monitoramento/Sistemas de gerenciamento de Ativos, Instrumentação e instrumentação de monitoramento da Saúde de Fábricas/Ativos.
Patrick também é o autor de várias patentes com aplicação direta ao monitoramento e diagnóstico de máquinas rotativas: US 6,705,168 B2 Processo e dispositivo para processamento das medidas de vibrações de rotores de máquina rotativa; 20160041068. Aquisição sem fio (Wireless) e Análise de Dados de Máquina (patente em curso); 20160041070 Diagnóstico Automático de Falha de Máquinas Rotativas com Indicação do Nível de Confiança (patente em curso).
Conheças as soluções em produtos e serviços oferecidos pela Vibmaster para a manutenção preditiva em análise e monitoramento de vibração.