4 Dicas para Implementar um programa de Confiabilidade Bem-Sucedido
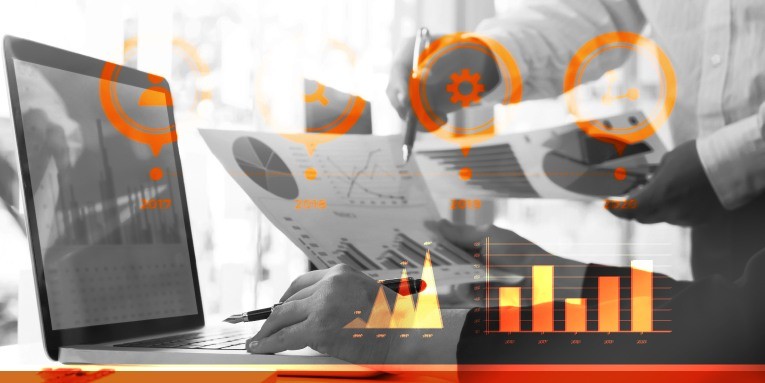
4 Dicas para Implementar um programa de Confiabilidade Bem-Sucedido
A implementação de um programa de confiabilidade em suas instalações pode trazer vários benefícios. Apenas alguns deles incluem:
- Maior eficiência
- Custos reduzidos
- Melhor organização
- Maior compreensão das tendências da máquina
- Menos frustração no local de trabalho
- Processo simplificado
A lista poderia continuar. Poucos de nós provavelmente discordam de que um programa de confiabilidade para suas máquinas e seus componentes é benéfico para a planta. No entanto, se um programa de confiabilidade não fornecer consistentemente resultados precisos, seu valor será reduzido significativamente.
A questão então é: como garantir que seu programa de confiabilidade esteja fornecendo consistentemente diagnósticos precisos?
Felizmente, existem algumas coisas que você pode fazer para garantir que o resultado do seu programa de confiabilidade seja um relatório preciso e eficiente.
-
Recomendamos primeiro priorizar o tipo de abordagem de manutenção a ser adotada: reativa, preventiva ou preditiva / proativa. Geralmente, a Manutenção Preditiva ou proativa é a melhor abordagem, mas em alguns casos (por exemplo, um motor de ventilador muito barato ou um ativo raramente usado), reativa ou preventiva pode ser apropriada. O ponto principal é adaptar sua abordagem de manutenção a um ativo e situação específicos.
-
Também é importante verificar ativos críticos regularmente e em um cronograma de manutenção. Se você estiver checando as máquinas quanto a rolamentos saudáveis, folgas, desequilíbrios ou qualquer outro número de fatores antes que a máquina esteja realmente tendo um problema, você terá dados valiosos para utilizar quando realmente precisar diagnosticar uma máquina com um problema. É muito útil ter conjuntos de dados diferentes da mesma máquina que você pode comparar para determinar onde está o problema. Quanto mais dados você coletar, mais precisamente você poderá analisar os relatórios atuais. Além disso, quanto mais dados capturados em um ativo ou problema, mais sua organização pode adotar uma abordagem proativa à manutenção e fornecer uma verdadeira solução de causa raiz.
-
Em seguida, sempre pergunte “por que”: por que os rolamentos continuam falhando em uma máquina específica? Por que um determinado ventilador ou exaustor continua tendo problemas com o desbalanceamento? Por que certas máquinas precisam de mais lubrificação do que outras? O uso de um exercício como o 5 Porquês para identificar a verdadeira causa raiz do problema permite a aplicação de ações corretivas e ajudará a evitar problemas futuros. Ao fornecer uma estrutura para um processo metódico de causa e efeito, uma ferramenta como o 5’Porquês também pode ajudá-lo a isolar qual parte do ativo está causando o problema, o que acabará por ajudá-lo a obter um diagnóstico mais rápido com menos frustração. Além disso, pensar na causa raiz aprimorará suas habilidades de pensamento crítico.
-
Verifique se você tem o pessoal certo para analisar as falhas em um processo. Treinamento é a chave. Quando novos funcionários são enviados para coletar e analisar a condição de seus ativos, verifique se eles estão acompanhados por um funcionário mais experiente, que pode oferecer orientação e garantir que o novo funcionário desenvolva bons hábitos. Se sua equipe precisa de treinamento, você pode conferir as nossas opções flexíveis de aulas de treinamento aqui. Em conjunto com o treinamento, a eliminação do que pode ser chamado de “conhecimento tribal” também é importante. Existem muitos profissionais de manutenção experientes que têm muito conhecimento armazenado, mas se eles não documentarem esse conhecimento e as melhores práticas, a nova geração de profissionais de manutenção perderá. Recomendamos encontrar uma maneira viável de transferir as informações valiosas mantidas por funcionários experientes para o seu CMMS, para que possam ser utilizadas por todos os funcionários. Parte disso pode incluir rotulagem consistente de ativos, utilização do recurso de código de barras, como no OneProd Falcon, e organização dos dados que você já possui.
Para todas as práticas acima, recomendamos organizar as máquinas por uma hierarquia de ativos e utilizar um sistema CMMS para salvar as informações da máquina em um local que seja facilmente acessível a qualquer pessoa que realize manutenção ou supervisione a manutenção em suas máquinas. Precisão e eficiência são a chave para o sucesso de um programa de confiabilidade, e esperamos que as etapas acima ajudem você a alcançar essas metas.
Leia mais assuntos complementares:
- Monitoramento Online: o Novo Normal na Manutenção Preditiva
- 10 Etapas Importantes de um Plano de Manutenção Preditiva
- Monitoramento sem fio de equipamentos: conheça o Eagle e o Falcon